Dinstock offers a wide range of finishes for its fastener products that meet fastener coating standards
including the following:
Plain self-colour finish
This bare metal surface has no finish for improving appearance or corrosion resistance, which is very low if the material is steel.
Often the surface has been oiled, which improves lubricity.
Plain finish fasteners can be used indoors or in outdoor environments where corrosion protection is not an issue.
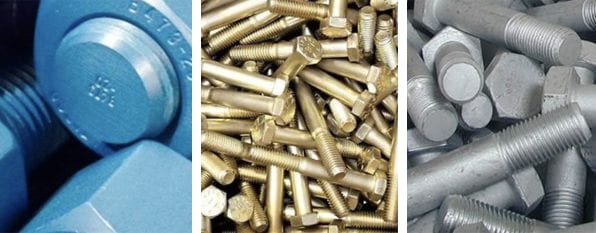
Zinc plating including coloured passivated finishes
Passivates/Chromates are used to coat metal parts in order to provide a longer life for the part. It is commonly used on zinc-plated parts in order to provide protection from corrosion such as white rust or red rust. Chromates can come in many different colour variations: clear, blue, yellow, or black.
Hot dipped spun galvanised
Fasteners are placed in baskets to be galvanised then immersed in molten zinc at a temperature of around 450°C until the temperature of the work is the same as the zinc. During this process, the molten zinc reacts with the surface of the steel to form a series of zinc/iron alloys.
Sherardising
Sherardising is the formation of a corrosion-resistant, zinc-iron alloy coating, on the surface of steel or iron. The method involves the heating of the object in an airtight container that has zinc powder.
Zinc flaking
Zinc Flake is a non-electrolytic plating process which offers very high corrosion and chemical resistance. As a result, there is a low risk of hydrogen embrittlement which makes it particularly suitable for fasteners with a tensile strength greater than 320 HV.
Geomet is Dinstock’s preferred Zinc Flaking process
Xylan
Xylan coatings are dry-film lubricants combined in a matrix with high-temperature organic polymers developed to provide unique and desirable properties. Xylan coatings provide lubrication and controlled friction, wear resistance, heat resistance, non-stick and release properties.